Case Study Regarding Material Handling
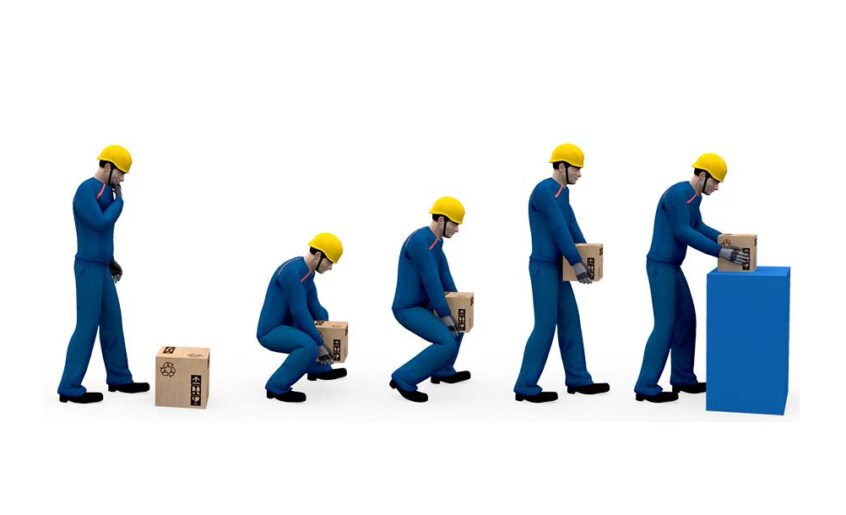
Volume 4, Issue 2, April – June 21
Case Study Regarding Material Handling
Sourav Chakraborty
B.Tech (Elec. Engineering), SMISE
Email id: souravc618@gmail.com
Abstract
Case Study is important analysis to identify cause of accident and ensure safety control measure of such accident to prevent future accident. Case study also shares during training or meeting or other program among employees to aware them. This Study is carried out to know material handling related risk and their safety measure. In This study one Incident investigation report is included to know the cause and how to prevent such accident.
Keyword: Case study regarding material handling, Safety Measure during Material handling, Potential causes of accident related to material handling, Risk control.
Objective
- To plan and identify safe method of material handling
- Identify potential source of harm that associates with material handling activities
- Identify causes of accident & Ensuring adequate safety Control measure to Prevent such accident
- To create more awareness among employees
- To control work place risk
1. Introduction
Material handling is major job that run in majority of industries. Several types of risk such potential of personnel injury or other harm are associated with material handling job. Safety or health safety Environment (HSE) term is very much famous with industrial instruments or equipment’s which are used in daily basis to measure or to maintain every parameter that are directly linked with SAFETY. Material handling plays an important role in various industries to maintain safety standards in all aspects as well to ensure comfort of operator or worker who is directly connected with the job. Material handling is the positioning and placing of any materials in an industry for business purpose or too some extent. Now -a-days manual handling has been reduced by uses of several machines. Automation is playing major role for reducing of manual handling.
Manual handling is generally of two types; manual handling and mechanical handling. To prevent material loss, time loss, accident due to manual handling, mechanical handling is the best preference. We will discuss here regarding common issues of material handling and its impact in safety and their respective reports. By defining case study, we will try to understand the difference of mechanical handling. Corrective measures will also be discussed and their sequence of work to mitigate the accident as discussed in the case study in the most possible way.
2. Need of material handling
- Movement of materials from one place to another
- To increase the production rate by using of mechanical handling.
- Material handling process is used to load and unload of vehicle.
- For storage purpose we prefer material handling.
- Now-a -days mechanical handling more increased as in manual handling may some physiological problem occurs due to not maintaining proper SOP.
- Lifting process easier than previous.
3. Hazards during material handling
- Carrying of excessive load
- Improper lifting process
- Defective or non-standard material handling equipment
- Doing work by non-maintaining of proper safe operating procedure (SOP}
- Not wearing of proper PPE
- Slip and trip
- Improper housekeeping
4. Method of Lifting or Material Handling
Material Lifting method may be manually or Mechanical means
4.1 Method of manual lifting
- One foot ahead of the other in the direction of movement
- Pick the load from the palm
- Keep the back side straight
- Keep the load close to body
- Head must be in correct position
- Vision should be clear
4.2 Method of mechanical lifting:
- Proper equipment to use
- Proper rated equipment to use to lift the load
- Safe working Load (SWL) to be check
- Pre inspection checking to do
- Proper identification mark to use
- Regular preventive maintenance to do
- Parts to be changed as per OEM guideline
- Speed of equipment to be monitored and to be controlled
- Properly trained professional to be engaged
- Training schedule to be maintained for operators properly
- Operator knowledge to be clear about related hazards
5. Advantage & Disadvantage of Mechanical handling equipment
5.1 Mechanical handling advantage:
- Physical stress on human will be less
- Productivity will be increased
- Efficiency will be increased
- Easy and fast handling of product
- Reduce rate of accident
- Better and time to time customer service
- Better marketing
5.2 Mechanical handling disadvantage:
- Initial cost will be more
- Restricted flexibility of changes
- Chances of machine failure
- Productivity may get affected for long time
- Maintenance cost is very high
- Totally depends on machine
6. CASE STUDIES
A case study included here of a company where accident happened during material handling operation. In this case study, Name of Company & Injured person name has been hide due to company data policy.
Company Name-ABC, Location- Najafgarh, Delhi handling warehouse operation by using of 8 Nos of forklifts for material management, loading and unloading operation. During loading of Block-A, Forklift no-4 when carrying pallets of 20T (Load with 12 blocks), the pallet got break and due to the heavy load of materials two of operators were seriously injured and almost 10T product damaged.
Reporting Proforma
COMPANY NAME- ABC INFRASTRUCTRE & ENERGY SERVICES LTD, DELHI
Accident Investigator Details
Name: – Sourav Chakraborty | Reporting date: – 12.04.2021 |
Designation: – Manager | Reporting time: – 16:00 hrs. |
Department: – Maintenance | Place: – Najafgarh, Delhi |
Accident / Incident details
Brief description: – During loading of Block A (South side of warehouse), Fork-lift No-4 carrying the pallet with 12 individual blocks got break and due to the heavy load of the materials two of operators got injured. Out of 12, 6 Nos of block directly hit the operators. Site-in-charge Immediately stop the loading procedure and rescued the respective persons for the further treatment. Total of 10T approx. products damaged due to this. Loading remains stopped for 3 hrs. |
Time of Accident/Incident: – 15:10 hrs. |
Location: – Block-A front side section 232A |
Injured Person details: – Mr. Sanjeev & Mr. Praveen from M/s. Infotech Pvt Ltd (Vendor ID- 0027729) |
Work permit Number/ Type: – NA |
PPEs being used: – Yes |
Any specific damage: – 10T approx. product damaged. |
Type of Injury: – Material bags & pallet pressure directly to the whole part of the body. Bone (Right hand of Mr. Sanjeev and Right leg of Mr. Praveen) damage |
Sequence of Events
- Loading operation continuing at block-A (South side)
- Infront of loading operation block 232A was there for material storage.
- Forklift No-4 going to take the full pallet load of 20T.
- That time the pallet got break.
- Out of 12 blocks, 6 blocks directly hit two operators assisting the loading operation.
- Operators got seriously injured, immediately rescued them and sent to nearest hospital.
- 10T approx. products damaged.
- Later area cleaned and normal the operation.
Possible Root Causes
- Pallet inspection was not done.
- No identification mark was there.
- Pallet condition was not good.
- Excessive load was there as per pallet condition.
Corrective Measures
- Provide training related to inspection and checking.
- Provide refresher training to all operators.
- Review inspection program.
- Review work procedure.
- Identification marking to be proper.
- As much as low load to carry.
- Operators should maintain adequate distance from forklift as well during loading operation
6.1 Analysis
In above case-study we have seen that during forklift (mechanical handling) accident takes place for the several mistakes. Possible root-cause analysis also taken into account and their mitigation technique for safer operation. Brief analysis of this as below mentioned: –
- Proper inspection was not done for pallet.
- Pallet condition was not good.
- Immediate first-aid was required before sending the injured persons to Hospital.
- Site in charge daily safety-walk was missing.
- Distance from Loading block to material management block must be adequate.
- Lack of awareness observed related to this type of accidents.
- In a hurry word to be removed from this type critical area.
6.2 Recommendations
Following recommendations are below mentioned:
- Site in-charge to take site inspection and cross verify the critical location before starting of any job.
- Safety talk to be given to all operator on daily basis.
- Related topics to be covered in Daily TBT.
- Job safety analysis to maintain.
- Operator must be well trained and fit.
- Forklift related training to be provided to all operators.
- Work related video-graphic training also recommended.
- Being aware of work-related Hazards.
7. Conclusion
Case study is depth analysis of Accident, their causes and safety measure that can help to prevent similar accident. In simple, we can say that case study is a method of key learning & preventing similar future incident. Case study help to identify below parameter
- Investigation to do by considering most possible root causes.
- Possible mitigation technique to discuss regarding the accident prevention.
- Proper address to be there in investigation format.
- Material handling regarding training to be provided.
- Awareness to be build up amongst every worker.
- Maintaining of work area safe and healthy from each and every aspect.
- Necessary standards and compliance to follow.
- Job safety analysis to be done related each and every critical work.
- Video-graphic training to be conducted regarding condition monitoring.
- In daily TBT and safety talk, these topics to be covered.
Reference:
Study on Site Accident