Effective Handling of Fluids and Liquid Metals Using IoT
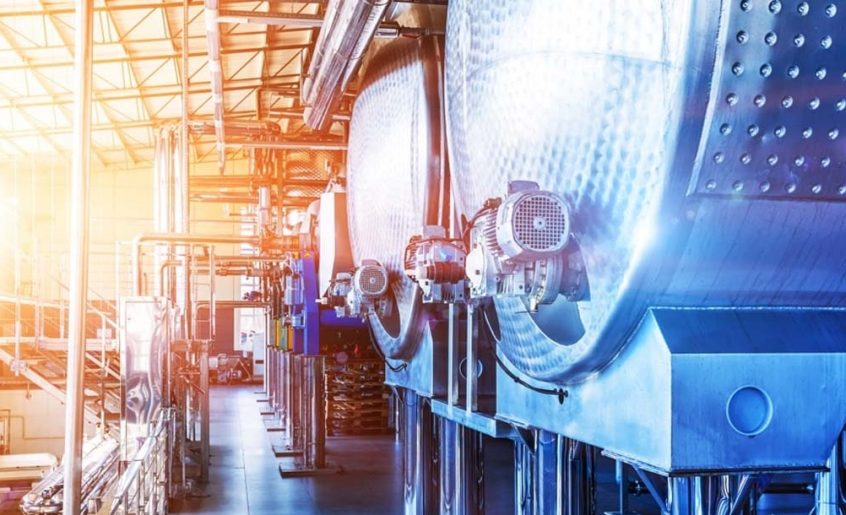
Volume 3, Issue 1, January – March 20
Effective Handling of Fluids and Liquid Metals Using IoT
Praveen Sankarasubramanian1 [0000-0001-7711-9040]
1Research Scholar, Vels Institute of Science, Technology and Advanced Studies (VISTAS), Chennai, Tamilnadu, India.
Email id: praveengrb@gmail.com
Abstract
Fluids and Liquid Metals (FLM) are widely used in industries like steel plants, chemical industries, and nuclear reactors. Handling Fluids and Liquid Metals are a crucial task[5]. Pipelines, propane bobtail trucks, boilers, gas cylinders widely engage with the liquid metals. The structure of the equipment and pipelines designed to withstand several environmental conditions. However, these leakages are the major causes of innumerable losses in nature and industry. FLM leakage can result in serious ecological disasters. This paper discusses the FLM leakage detection mechanism and framework to achieve this. It is hard to avoid the FLM leakage. However, in order to reduce the impact on the environment, it is important to monitor and detect the fire or any other hazards in a timely manner. Early detection of leakages will allow quick responses to avoid FLM discharge.
Keywords: FLM, IoT, SVM, CNN, DNN.
1. Introduction
Transportation and Handling of fluids and liquid metals considered as a major process in industries. Estimated deaths due to transportation of fluids like petroleum products are higher using trucks, ships and rails [6]. The loss due to pipeline [1] leakage incidents is enormous [7]. In the year, 2010 Nearly 8 people killed due to the explosion of a petroleum pipeline [8]. Many fire detection systems generally have simple sensors. This system will have lower accuracy and are sensitive to the sensor failure [2]. For example, sensors like smoke sensor could send false information about heavy dust as smoke.
Existing systems uses physical observation of the FLM chambers or pipelines. Industry could use standard rule based observation sheets. Alternatively, it could be integrated with traditional PLC or Instrumentation based control systems. It is impossible for a normal user to calculate the threshold value and find a dynamic prediction.
This paper aims to identify the different sensors used to handle and monitor the state of FLM. Section 2 describes the different sensors selected for the monitoring process. Section 3 describes the process of collecting the sensor data, preprocessing it and using Multi AI Technique to do an adaptive prediction and warning system.
2. FLM Leakage Detection Using Sensor
Multiple techniques proposed during last decade. Existing detection techniques categorized as
- Local and Remote sensing
- Hardware and Software sensing
- Ocular / biological sensing
- Manual sensing with experienced professional
- Visual Testing
- Unmanned vehicles or remotely operated vehicle
- Surface and Internal sensing
Surface level and internal sensing is further subdivides as,
- Surface level
- Sound based sensing,
- Electromagnetic sensing
- Light based sensing
- Impedance sensing
- Reflection sensing
- Fiber optical sensing
- Vapor sensing
- Radar based sensing
- Ground penetration
- Light detection and ranging (LIDAR) sensing
- Internal Sensing
- Pressure sensors
- Digital signal processor
Next subsection briefs out about the various sensing technique.
2.1 Sensing Techniques
Surface level testing /(Acoustic Pulse Technique): Uses fixed frequency range of pulse transmitted on the surface of the pipeline. The delta (difference between the sound pulse and reflected sound pulse) should be constant. The deviation in the delta denotes the existence of leakage. This approach is active or push mechanism where signals directed from the SIGNAL EMMITING SENSOR → EQUIPMENT → ECHO DETECTING SENSOR. Another method is passive or pull mechanism where frequent pulse received from the equipment. Current signal frequency compared with the historical data. If DELTA is approximately 0, then there is no leakage else leakage is present. This system is easy to handle, cost effective and suitable for early detection. However, sensitive to random environmental noise and false alarm triggered.
Fiber Optical Sensing System: Identifies the abnormalities through temperature change in the optical properties of the cable induced by the presence of leakages or cracks. Optical Fiber can act both as sensor and data transmission medium.
Vapor Sampling Methodology: This is applicable in gas tank systems. This methodology helps to identify the small cracks and leakages. Coupling vapor-sampling sensor with other sensors improves the sensing time and provides faster response time.
Infrared Imaging Thermography Camera: Detects the temperature difference in gas tank. This methodology is contactless and non – invasive approach. It is applicable for various condition monitoring application such as heat transfer, tensile failure. This is a highly efficient power for transforming detected objects into visual images, easy to use and process images
Ground Penetration Radar: Ground Penetration Radar is a tool to detect and identify physical structures like buried tanks and pipelines. This is a non-invasive approach utilizes electromagnetic wave propagation and scattering technique. GPR signals are best in timely detection of leakage in underground pipelines, reliable and leakage information is comprehensive. Easily distort this signal in a clay soil environment.
Light detection and ranging sensor: It employs pulsed laser. This technique used for the detecting methane leakage.
Ultra-Light Sensor:Light or fluorescence method uses higher intensity light sources of a specific wavelength for a molecule excitation. Detection of leakage implemented by unfiltered ultraviolet light.
Piezo Electric Transducer: Piezo electric transducers patched on the surface of the equipment or pipelines. Electromechanical Impedance changes with respect to the position of the equipment. Impedance at leakage prone area is different from the normal area.
Capacitive Sensing: Measuring changes in the dielectric constant of the medium surrounding the sensor and used in environmental monitoring. This is best for subsea equipment monitoring. Sensor sensitivity with respect to the leakage size is dependent of the distance between leak position and drift of the leaking medium.
Ocular / Biological Sensing: Ocular/Biological methods uses trained dogs, experienced professionals, smart pigging, drones.
Trained professionals walks around the pipelines, storage tanks, bobtail containers recognizes the cracks , leakages by visual observation or smelling the odor coming out of the crack points. Trained dogs are more sensitive to the change in odor. To improve the observation trained dog monitors with the trained professional.
Remotely Operated Vehicles (ROV) like autonomous underwater vehicles and drones used for remote monitoring. It reduces the extent of human causality. Number of ROV are available for monitoring hazardous environment. This method has higher operational safety is an advantage of unmanned vehicles.
Interior Methods: Interior methods are classified as pressure based and digital signal processing based
Pressure Senso: System continuously monitored and status conveyed to centralized console. Pressure, Flow rate, Temperature, density, volume and other parameters monitored and sent to the Multi IoT Framework. Pressure drops and varies in a closed environment. Proper pressure maintained in the chamber or pipeline and monitored continuously.
If surface pressure == interior chamber pressure, called neutral pressure. If surface pressure > interior pressure then it is called positive pressure. If surface pressure < interior pressure then it is called interior pressure. If leakage occurs, pressure alters and flow speed changes. This negative pressure information sent to Multi IoT Framework and suitable action taken.
Digital Signal Processing: First step is the data acquisition process. In data acquisition process, internal pressure and flow of the fluid is measured. Next step is pre-processing step. Pre-processing step filters the background noise and makes effective feature extraction.Various feature extraction steps employed to extract feature. Extracted feature (pattern) compared with the historical pattern and used for the decision-making. If the compared result is beyond the threshold value alarm triggered.
3. IoT Framework for Adaptive Prediction and Alerting
Behavior of an engine or chamber or boiler or any industry unit might change according to the environmental temperature. Data sensed in same place may change from time to time. Maintaining a static threshold value is not a right option. The dynamic threshold is best for achieving an adaptive prediction and alerting system. It is impossible to calculate the threshold and apply it.
Extraction of feature data from the sensor data is a difficult task. This task simplified by using Artificial Intelligence.
The module Fig 2 has three sub modules
- Data Ingestion Framework
- Context Based Pre Processing
- Multi – AI Based Adaptive prediction framework
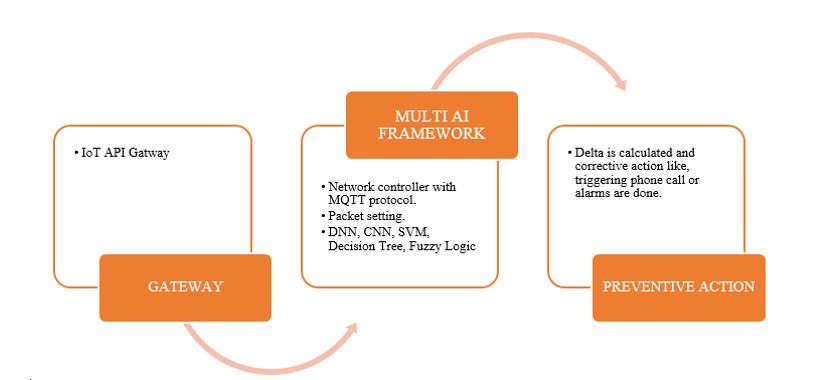
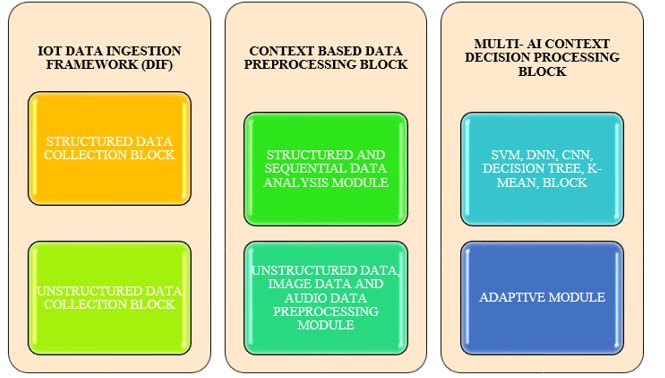
3.1 Data Ingestion Framework
The proposed detection system collects data from multiple IoT gateways (fig 1). IoT API gateway collects the data from heterogeneous sensors sent to a multifunctional intelligence system. IoT Middleware components like MQTT has the ability to connect with various devices [9, 10, 11, and 12]. IoT Middleware connects various devices and transmits data in large-scale IoT systems. TCP based MQTT protocol.
The sensor feeds collected, sent to the context based preprocessing block.
3.2 Context Based Preprocessing
This context based preprocessing block has multiple Machine Learning algorithms. The selection of algorithm and order of execution could differ from data to data [4].
Sequential data, Text data, Structured, unstructured are separated and processed by respective module. Effective analysis of heterogeneous data achieved by using multiple Machine Learning algorithms.
3.3 Multi Ai- Based Predictive Framework
ML Algorithm framework divided into shallow learning and deep learning. Shallow learning used for categorizing sensor data. Support Vector Machine (SVM), K-Means Cluster and Decision Tree used to classify and aggregate the sensor data. A deep learning network used to quantify the data and image. Deep Neural Network is used to determine the current value through quantify data and analyze the changing situation through continuous data. Data collected over a period of time hence, immediate data detection is difficult. DNN used to measure the changing situation. Convolution Neural Network analyzes the situation by detecting features in image data. Fuzzy algorithms express the closeness to each situation.
Multiple machine learning algorithms like neural networks, adaptive fuzzy algorithm.
4. Conclusion
This suggested paper list of leakage detection sensors classified and briefed out. Sensors like acoustic sensors, visual monitoring, impedance sensors, fiber optic sensors, and infrared thermal camera are listed. Next, the section describes the data acquisition framework from different sensors with the help of the IoT gateway. Context-Based Data preprocessing block grouped the collected results based on a context. Adaptive analytics has done with the help of the final framework. This proposed approach looks efficient, robust and simple. It suggests a way to handle and mitigate the hazards created due to the Fluids and Liquid Metals. In addition, earlier detection of leakages is achievable and detection of hazards monitored in a timely manner.
References
- Adegboye, M. A., Fung, W. K., & Karnik, A. (2019). Recent Advances in Pipeline Monitoring and Oil Leakage Detection Technologies: Principles and Approaches. Sensors (Basel, Switzerland), 19(11), 2548. doi:10.3390/s19112548Author, F., Author, S.: Title of a proceedings paper. In: Editor, F., Editor, S. (eds.) CONFERENCE 2016, LNCS, vol. 9999, pp. 1–13. Springer, Heidelberg (2016).
- Park, J. H., Lee, S., Yun, S., Kim, H., & Kim, W. T. (2019). Dependable Fire Detection System with Multifunctional Artificial Intelligence Framework. Sensors (Basel, Switzerland), 19(9), 2025. doi:10.3390/s19092025
- Sampath, S., Bhattacharya, B., Aryan, P., &Sohn, H. (2019). A Real-Time, Non-Contact Method for In-Line Inspection of Oil and Gas Pipelines Using Optical Sensor Array. Sensors (Basel, Switzerland), 19(16), 3615. doi:10.3390/s19163615
- Praveen Sankarasubramanian, Dr.E.N.Ganesh, “Algorithm to Identify the Connection between Sentences”, International Journal Of Information And Computing Science, Volume 6, Issue 7, July 2019,158 – 162 ISSN NO: 0972-1347 DOI:16.10089.IJICS.2019.V6I7.18.3248
- Praveen Sankarasubramanian, Dr.E.N.Ganesh, “IoT Based Prediction for Industrial Ecosystem”, International Journal of Engineering and Advanced Technology (IJEAT) ISSN: 2249-8958, Volume-8 Issue-5, June 2019
- Cramer R., Shaw D., Tulalian R., Angelo P., Van Stuijvenberg M. Detecting and correcting pipeline leaks before they become a big problem. Mar. Technol. Soc. J. 2015;49:31–46. doi: 10.4031/MTSJ.49.1.1
- Liu J., Yao J., Gallaher M., Coburn J., Fernandez R. Study on Methane Emission Reduction Potential in China’s Oil and Natural Gas Industry (Technical Report) RTI International; Research Triangle Park, NC, USA: 2008.
- Lena V.G. Pipelines Explained: How Save Are American’s 2.5 Million Miles of Pipelines. [(accessed on 28 February 2019)];2012 Nov 15; Available online: https://www.propublica.org/article/pipelines-explained-how-safe-are-americas-2.5-million-miles-of-pipelines
- MQ Telemetry Transport. [(accessed on 12 March 2019)]; Available online: http://mqtt.org.
- Bormann C., Castellani A.P., Shelby Z. Coap: An application protocol for billions of tiny internet nodes. IEEE Internet Comput. 2012;2:62–67. doi: 10.1109/MIC.2012.29. [CrossRef] [Google Scholar]
- Fielding R., Gettys J., Mogul J., Frystyk H., Masinter L., Leach P., Berners-Lee T. Hypertext Transfer Protocol—HTTP/1.1. IETF RFC 2616. [(accessed on 30 April 2019)];1999 Available online: https://www.rfc-editor.org/rfc/rfc2616.txt.
- Klauck R., Kirsche M. XMPP to the rescue: Enhancing post disaster management and joint task force work; Proceedings of the 2012 IEEE International Conference on Pervasive Computing and Communications Workshops; Lugano, Switzerland. 19–23 March 2012; pp. 752–757. [Google Scholar]