Work Environment Toxicity Assessment at Workplace
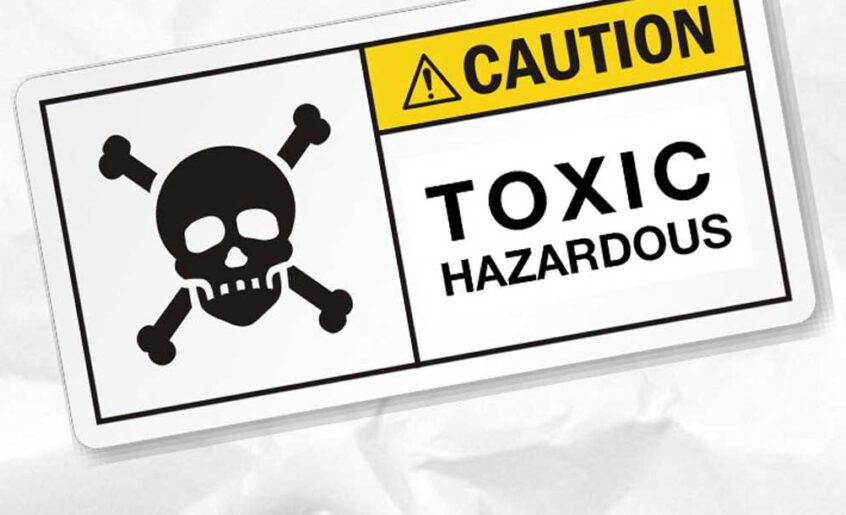
Volume 4, Issue 1, January-March 21
Work Environment Toxicity Assessment at Workplace
Shahnawaz Rampuri
B.Tech (Elec. Engineering)
Email id: shahnawaz.rampuri2@gmail.com
Abstract
Poor air quality of work environment always effects to personnel health. In industries, during storage, operation and process facility several hazardous agents emit and spread in work environment and pollute them and such poor quality of air effects to human health as well living things. In this Study, A work place air quality assessment is carried out and effective method has been recommended to risk control or minimization. This paper is very helpful to know effective procedure of air quality assessment. In this paper air quality is concern with toxicity and show work place air quality is satisfactory or not. So, air quality and work environment toxicity represents same meaning in this paper. This Study is conducted to Assess work environment Toxicity during Storage, handling & Process facility operation in industries to identify associated risk with personnel health of people, environment and their characterization. In this paper basically study focus to Particulate matter (PM10, PM2.5), Carbon mono-oxide (CO) & Air quality index (AQI). A Study summary including air quality parameters of Alternative Fuel and Raw (AFR) materials handling site, also included in this article.
Keyword: Work environment Toxicity Assessment (WETA), Air quality, Hazardous work environment, Control Prevention, Procedure of WETA, WETA report Preparation
Objective
Following objectives has been considered in focus while conducting the Assessment:
- Identify Risk of exposure to personnel health & environment due to poor air quality
- Check to existing safety control measure is adequate to minimizes risk as low as reasonably Practicable (ALARP).
- A systematic, critical appraisal of all potential hazards related to toxicity involving environment, personnel, plant, services, operations and procedures at workplace in industries.
- To ensure that effective occupational health safety system to fully satisfy the statutory requirements as per respective state or country rules, regulation and codes.
1. Introduction Work Environment Toxicity Assessment
Work place Air quality is important parameter to ensure personnel health of people in industries. In industries, several types of dust, fumes & gases emit during material storage, operation and process facility and mix with air and pollute them. Formaldehyde (HCHO), Total volatile organic compound (TVOC) outdoor, Carbon mono-oxide (CO), Carbon-dioxide (CO2), Particulate matter (PM10 or PM2.5), Nitrogen oxide (NOX), Sulphur oxide (SOX) are few examples of agents, if they exceed beyond permissible value in work environment, then harm to personnel health and environment. Poor air quality exposed to personnel health through inhalation and may lead to cause of respiratory related illness or harm to others organ of human. The work environment Toxicity assessment is simply the characterization of the potential adverse effects on the safety and health of employees, the public, property and the environment in general. This work environment Toxicity depends on different factors such as product, physical and hazardous properties, handling procedures, storage conditions, duration of exposure and existing control measures, necessary to minimize its adverse effects. In this paper, workplace Toxicity is concern as poor air quality.
Work environment Toxicity Assessment helps to identify materials/products storage, handling and process facility related risk associated with personnel health at work place in industries and their characterization. Effective method always helps to identify potential adverse health effects, potential sources that can harm to environment and adequate safety control measure. As part of the work environment Toxicity assessment, Air quality samples are tested at work place of different location to evaluate health risk. Inadvertent using of hazardous product at work place can result of Occupational Health diseases due their exposure. In addition, Hazardous agent generates from products and process facility and mix with air to environmental concerns and threat to the health and safety of employees. A majority of these health related incidents involved routine frequently performed procedures. Their occurrences can only be attributed to improper material storage, handling, labeling, inadequate training, and/or lack of updating or improving work procedures. There is possibility of health problem when not follow safety norms during working at poor air quality hazardous work place. To ensure personnel safety and probability of environmental impact of such incidents are minimized, a work environment Toxicity assessment, which includes products/ Process study and evaluating work environment toxicity related risk at workplace in industries. There may be different route of exposure of personnel of work environment toxicity such as inhalation, ingestion, injection or direct contact with skin. In this paper basically cover to such agent that can be exposed to personnel health through inhalation.
2. Work Environment Toxicity Assessment Procedure
The work Environment Toxicity Assessment in any industries is performed as per the standardized ISEI Methodology, which comprises six steps as shown in Table 1. The objectives of these steps, descriptive parameters and the methods followed to achieve the assessment are also listed in the table 1. Steps can be increase or reduce as based on requirements and study.
Table 1: Work environment Toxicity Assessment (ISEI methodology)
Steps | Description | Objective | Methods |
1 | Identification of Products / Materials/ Process | Obtain an inventory list of all productsRecognize hazardous propertiesProcess identificationTo identify hazardous emission or agents | Process reviewWalk-through inspectionInterview pertinent personnelReview Material Safety DataSheets, and waste profile reference of materials |
2 | Storage Facility & Condition | Signs and accessibilityAuthorized personnel onlyArea conditionsVentilationCompatibilityContainers type (sealed / open)Spills and leaks contingency plans (decontamination)Shower facilitiesPersonal Protective EquipmentLabeling and proper hazard warningCHBs and PostersRecord keepingFire extinguisherFirst aid facility availability | Physical Inspection & Record verificationInterview pertinent personnelConsult company standards and reference materialsStorage Facility structure including tank, pipelines stability verification |
3 | Method of Transfer & Handling | Closed versus open systemsEmployee exposure riskCaution LabelingChemical Hazard Bulletins and PostersPersonal Protective EquipmentTraining and work practice | Walk-through inspectionInterview pertinent personnelProcedures review of loading / unloading for bulk-delivered productsExposure assessment as warranted |
4 | Control Measure include PPE’s | Whether they are requiredAvailability and conditionsWhether they are requiredAvailability and conditions | Walk-through inspectionProcess review to determine feasibilityInterview Pertinent PersonnelCompliance of OHS element |
5 | Medical Health Check Up & Record | Whether Medical Health Check up ConductedCompliance of Medical Facility | Inspection & recordInterview Pertinent PersonnelRoutine medical health Check up of employees those engaged in AFR handling siteAvailability of Certified Medical staff and resources |
6 | Air quality Assessment & Toxicity related Risk Classification | Recognize high, medium and low risk of work place Toxicity Establish special procedures for handling high-risk products | Review data from the above stepsAir Sample Collection and measurementDetermine compliance with Govt. Guidelines & standards |
2.1.1 Identification of workplace storage products/materials, Activities and their Hazardous Properties
In this stage, Products, activities and their hazardous properties has been identified through workplace visit. All details of Products and process activities data should be collected and study conducted to know the properties of materials and potential risk at work place. The work place Toxicity related hazard ratings can be determined from Chemical Hazard Bulletins (CHBs), Material Safety Data Sheets (MSDSs), waste profile, Workplace monitoring and/or other related reference materials. On based on Material or generate waste or agents generated during process can be identify and categories in hazardous and non-hazardous. During the assessment, need to note down to raw materials that used during process facility & operation. List out to materials as per Table 2.
Table 2: Lists of Materials / Products
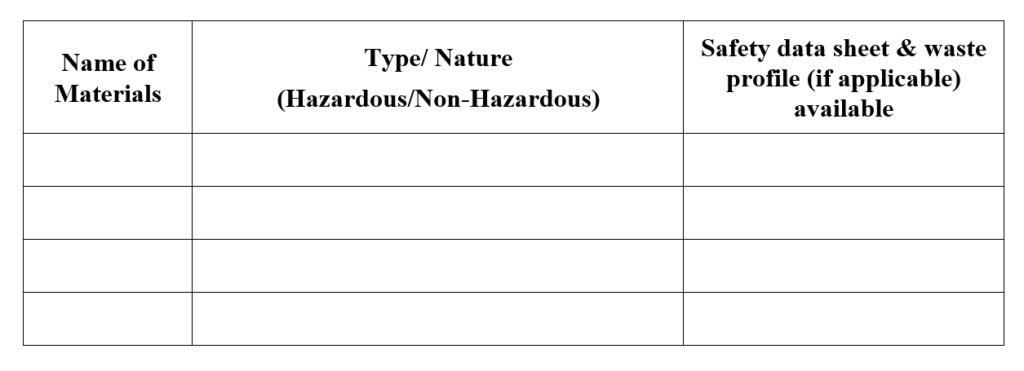
2.1.2 Storage Facility & Condition
In this section, storage facility & Condition has been checked. As per nature of waste, waste storage area should be categorized to store waste materials. Waste material available may be in form of solid, liquid or gas. When materials received from supplier, and emptied in such area. Need to access exposure assessment to personnel that are engage in their work in storage area. Potential exposure to person depends on existing safety control measure, Toxicity of material and air quality status of work environment.
Table 3: AFR Materials weight, storage & Transportation (Handling) Summary
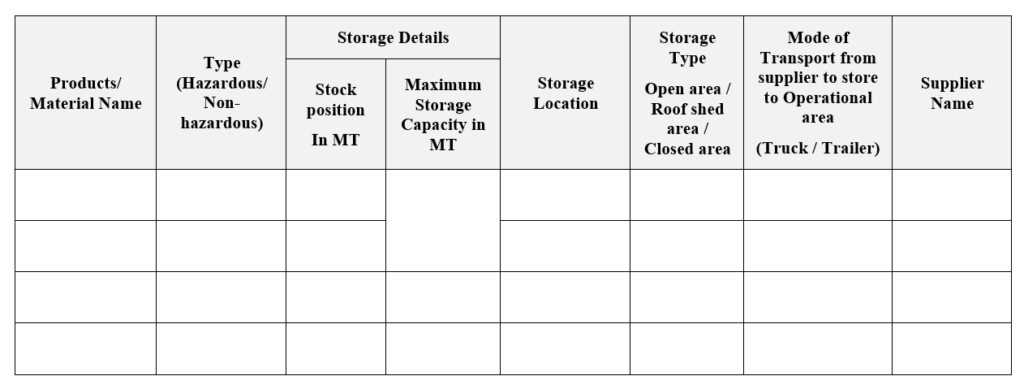
2.1.3 Method of Transfer & Handling
In this stage, need to find details information regarding supplier, method of Transport and handling to materials. Materials can be transport through Trailer, container, Rail or other means to origin to plant. In Industries, solid material can be transfer manually, through conveyor or other means and liquid materials can be transfer through Pump, pipe, container or other means. In this stage, study is carried out to know potential personnel health effect and harm to environment during Transfer and handling.


Fig. 1: Waste handling & Process Facility
2.1.4 Medical Health Check Up & its Record
Employees health check-up records of Occupational health center (OHC) helps to identify previous health disease. Such disease may be results of any hazardous agent exposure due to inhalation shall be check by assessment team. Availability of Occupational health center (OHC) help to examine employees regularly to identify and diagnose toxicity related illness or diseases in early stage. So, Previous illness record help to find hazardous agent availability at work place and OHC help to minimizing such risk. On based on these, study can be conducted to know air quality status at work place in storage and process facility area of industries.
2.1.5 Air Quality Analysis & Toxicity related Risk Classification
To Identify Airborne contaminants in air, Test to different parameter of air quality such as Oxygen, CO, HCHO, TVOC (Indoor & Outdoor), Particulate Matter (PM), Air quality index (AQI) and based on these obtained results, evaluate to associated risk with air quality of work place. If air quality will be poor then there will be risk of exposure to personnel health. Work place air quality can me monitor through Air quality monitor, Multi gas detector or other digital instruments to measure H2S, CO, PM10, PM2.5, HCHO, AQI likes parameters to identify to air. A standardized criterion can be use to characterize the risks pose at work place to be identify products and process facility at site. Accordingly, to products/materials or process that area using at workplace can be classified as hazardous and non-hazardous, or whether special handling procedures are required for each class. Factors which were considered in the stated standardized criteria included the hazard ratings of the product, quantity storage capacity and conditions, handling procedures, potential risk of employee exposure, duration of works, likelihood for leaks or spills and the presence and/or lack of safety control measures. On based on air quality analysis, physical walkthrough inspection & record verification, Air quality can be identify. Work environment toxicity risk can be identify and categories into low, medium or high or satisfactory and unsatisfactory.
3. Study Overview & Results of Air quality parameter on based on Assessment at AFR handling site in integrated cement plant
A work environment Toxicity assessment was carried out at AFR handling site in an integrated cement plant. Name of plant not included here due to mutual agreed with ISEI & respective company to not open name. In AFR handling & Process Facility area, Plastic waste, Pharmaceutical waste (Liquid & Solid), Spent carbon, Paint sludge, Agree waste, wooden dust, MSW, ARETP were using in which their few materials were hazardous and few were non-hazardous nature. Due to few limitations, details properties with name of materials not including here. Two Types of System were available there, solid AFR handling system & liquid AFR handling system. On based on Air quality analysis and physical walkthrough inspection of different location of material storage and process facility area and verification of records, different area are categorized in Two ways
- AFR handling site A: Air quality at work place is satisfactory
- AFR handling site B: Air quality at work place is un-satisfactory
AFR materials classification and specific action requirement as per standard include developing special handling procedures, employee awareness training, container labeling, engineering control and administrative control measures is considered during work environment toxicity related risk evaluating as per Fig. 2.
It needs to be emphasized that the degree of a risk posed by a given at AFR handling site (B) area can be minimized if special handling procedures are developed and implemented for the safe use of that product as per given recommendation and existing control measure should be available regularly.
3.1 Work environment air quality Status at AFR handling site
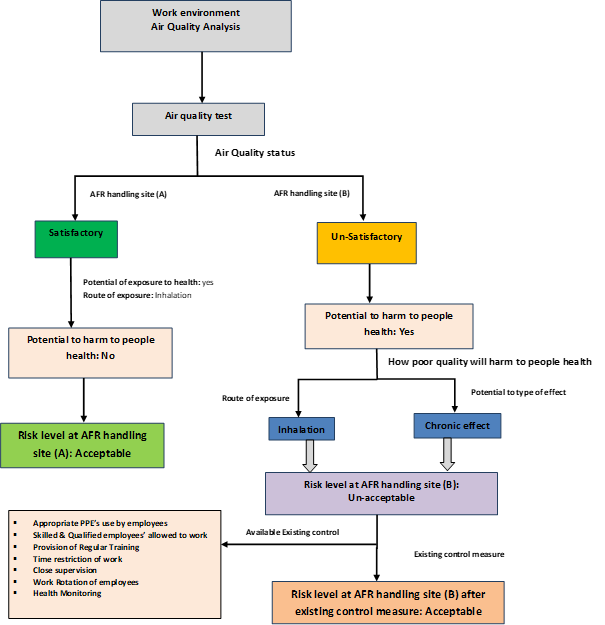
Fig. 2: Risk Level at Area A & B
Air quality of AFR handling site (A) area is satisfactory and Air quality of AFR handling site (B) area is unsatisfactory and cause harm to personnel health, if any gaps in existing control measure and in this area the presences of hazardous agents in air were very less and this may effects to personnel health due to long term exposure, if any gaps exist such as not using is suitable respirator.
During walkthrough inspection by Assessment team, this was found that Shredder is programmed to prevent untoward happening in case of overload or any deviation. Double Flap Valves were provided for Safety Interlock, Shut off Gate provided to prevent possibility of any reverse flow from the Pre-calcine. Best practices adopted during waste material storage, transfer and handling, engaged workmen are well trained and they use appropriate PPE’s therefore No or less possibility of exposure of health-related risk.
It needs to be emphasized that the degree of a risk posed by a given AFR product/materials and process facility has been minimized to implement Safe operating procedures and take other necessary safety control measure.
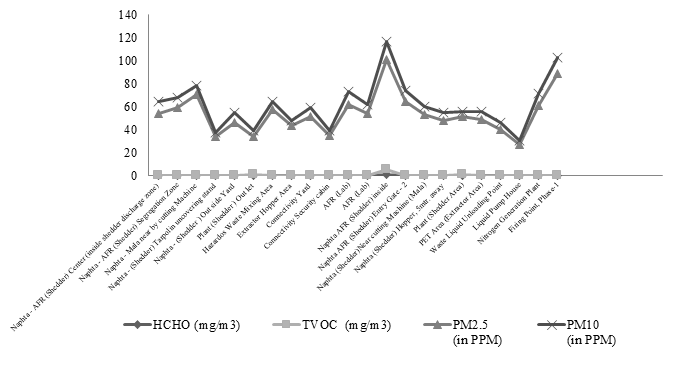
Fig. 3: TVOC (Outdoor), HCHO, PM2.5 & PM10 results at AFR handling site
3.2 Permissible Value of hazardous agent in work environment
Formaldehyde Permissible Value at work place is 0.50 PPM and 0.75 PPM is 8-hour exposure limit as Per OSHA. Average outdoor level 0.03 PPM is acceptable at work place. As per OSHA the permissible value of Carbon mono-oxide (CO) is 50 parts per million (ppm) for 8 hours.
Table 4, Air quality Parameter Exposure limit with permissible value
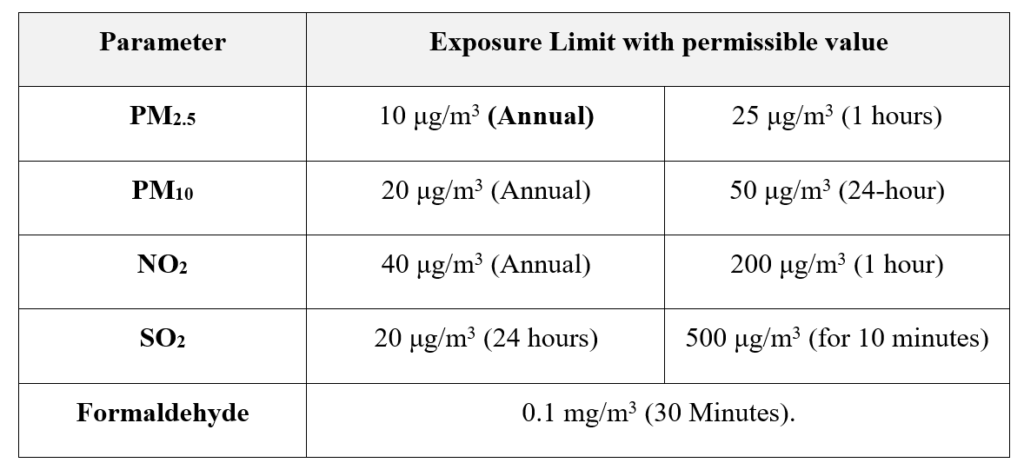
Sources: WHO guidelines
Table 5, TVOC levels and adverse health effects
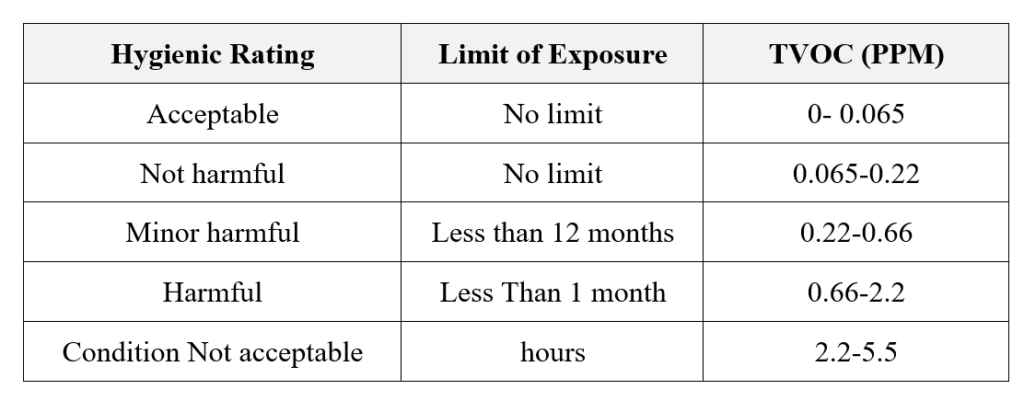
Sources: TVOC guidelines issued by the German Federal Environmental Agency
4. Summary & Discussion on based on AFR handling site
A work environment Toxicity Assessment (WETA) which includes AFR Product/ Process analysis was conducted at AFR handling site of an integrated cement plant unit on 20-21 Dec. 2019 and 31 Dec. 2019 to 1st Jan. 2020 in Gujrat state. The assessment was done in compliance with 41 F, Schedule II of Factories act 1948, HWR, EPA and Hazardous Materials Communication Program (HAZCOM)”. The work environment Toxicity Assessment was performed as per the standardized “ISEI work environment Toxicity Assessment Methodology” with the following:
- Company was taken applicable NOC and permission from state govt. and respective authority.
- Company was a very good record on worker safety and environmental management. This can be attributed to the management’s commitment in implementing and promoting corporate objectives on occupational health, safety and environmental goals.
- Company has won several award and recognition in field of Occupational, Health safety
- As per company policy, AFR team not accepts to such material or processes that have potential to create health risk or harm for environment. They check inventory, waste profile and analysis to sample. AFR Team follows all safety rules to control risk during AFR storage, handling and process facility.
- Periodic Health Check up conducted regularly (on every six month) for workmen and certified staff‘s available in OHC center including certified Doctor (AFIH qualified). Till date, No any Occupational Health related problem occurs at AFR handling site.
- Total Air quality sample collected from 24 locations from AFR handling site in which 20 location, No any risk found to pose of health risk for engaged employees. On Four location air quality was unsatisfactory. Oxygen level at work environment of all location was satisfactory and Carbon-monoxide, H2S was not found on any location of AFR handling site.
- At AFR handling site, few category of waste material has Hazardous nature that used at AFR handling site and Hazardous waste management plan (HWMP) was not documented properly to ensure compliance effectively
- All HAZCOM elements necessary to work safely with AFR materials / chemicals had been implemented. Material Safety Data Sheets and/or Chemical Hazard Bulletins were conspicuously posted in hazardous AFR waste/chemical handling areas. Elements of operating procedures for handling certain AFR products/Materials had been developed and implemented accordingly.
- Some AFR products that have potential to cause health effect had been identified prior to this assessment based on their hazardous properties, storage requirements, handling procedures and health risks. Relevant Operating Instruction Manuals have been developed to address health, safety and environmental aspects of such chemicals.
- Few chemical products were classified as medium-risk products. The need of special handling procedures for these chemical products is recommended. The remaining products were classified as low-risk products and their requirement for special handling procedures are of low priority.
- A chemical compatibility analysis was applied. This was necessary for the recognition of incompatible chemical products, which must not be mixed, stored and/or transported in close proximity to one another. The findings were arranged in a compatibility chart which readily illustrates and alerts employees of these products. Only high-risk chemical products were considered in constructing the chart.
- Recommend to supplier to submit safety data sheet of AFR products and materials that nature are Hazardous and driver competency details including Training record.
In general, housekeeping was good, a probable indicator of a committed and enthusiastic workforce. Personal protective equipment was suitable and adequate for the purpose. AFR team monitor CO, H2S, CH4& O2 Parameter on daily basis storage shed naphtha and plant. Safe operating procedures (SOP) & Hazard identification risk assessment (HIRA) prepared for AFR waste material handling and process handling. Over all observation ISEI Team found that risk is minimized As low as reasonable practicable to implement effective occupational health safety management system.
5. Conclusion: The aim of this study was to identify and evaluating probability of potential exposure of toxicity in work environment at AFR handling site or similar operation and process facility area. ISEI methodology has been used to measure and evaluate Toxicity in work environment and contaminants that were presence in air and it can results harm to personnel health. To evaluating work environment toxicity, basically focus to air quality that breathes by employees at AFR handling site. Air quality is monitored through digital air monitor and multi gas detector. HCHO, TVOC, PM 2.5, PM10, O2, like parameter has been measured of different location of AFR handling site and found air quality is satisfactory except Naphta AFR (Shedder) sub-part pre heater, Naphta AFR (Shedder) inside, Plant (Shedder) Mixing Area and Firing Point, Phase-1. Air quality unsatisfactory means contaminants are mixed with air and such contaminants can pose a significant health risk due to inhalation but such contamination in air have not potential to cause harm. This can be effect to personnel health due to long term exposure and if gaps in any existing control measure. Existing control measure at AFR handling site was adequate to control such risk upto Tolerable level.
Apart from this, AQI, H2S and CO also measured on different location of AFR storage, handling and operation facility area through Air quality Index meter and multi gas detector and found non-presence of AQI, H2S and CO in work environment at AFR handling site. Humidity and temperature at AFR site also measure and found satisfactory. Company were adopted best practices at AFR handling site to avoid any adverse health effect, employees use suitable personal protective equipments, un-authorised personnel entry is restricted and medical health check done time to time of all employees those are engaged at AFR handling process facility. Company AFR Team monitor CO, H2S, methane & O2 on daily basis on different location of AFR handling site. AFR Team Prepare SOP and HIRA for activity related to AFR handling and Process facility and ensure its strictly compliance as Per The Factories Act, India and respective legislation and codes.
Firstly, collect data and study to Storage and process facility, Need to identify potential route of exposure to person and effect to environment and based on this, plan and conduct Work environment Toxicity assessment. As per Institution of safety Engineers (India), 6 steps were used (Table 1) to identify work environment Toxicity but this is not limitation and steps can be reduce or increase as per requirements of applicable workplace. Material safety data sheet, waste profile of generated waste, consultation with employees, record of previous illness, air quality monitoring and visit at site helps to identify potential risk associated with work environment and exposed to personnel and control to such risk.
Reference:
- World Health Organization (WHO) (1993b). Biomarkers and risk assessment: Concepts and principles. Environmental Health Criteria 155. IPCS/WHO. Geneva: WHO.
- World Health Organization (WHO) (1994a). Assessing human health risksof chemicals: Derivation of guidance values for health-based exposure limits. Environmental Health Criteria 170. IPCS/ WHO. Geneva: WHO
- IGHRC (2004) Guidelines for good exposure assessment practice for human
- health effects of chemicals. (cr10) MRC Institute for Environment and Health, University of Leicester.
- IGHRC (2004) Guidelines for good exposure assessment practice for human health effects of chemicals. (cr10) MRC Institute for Environment and Health, University of Leicester.
- NIOSH (2005) NIOSH pocket guide to chemical hazards. Atlanta, GA, Centers for Disease
- Control and Prevention, National Institute for Occupational Safety and Health (NIOSH
- Publication No. 2005-149; http://www.cdc.gov/niosh/npg/, accessed 23 August 2010).
- Jayjock M (1994) Back pressure modeling of indoor air concentration from volatilizing sources. American Industrial Hygiene Association Journal, 55(3): 230–235.
- IPCS (1994) Assessing human health risks of chemicals: derivation of guidance values for health-based exposure limits. Geneva, World Health Organization, International Programme on Chemical Safety (Environmental Health Criteria 170; http://www.inchem.org/documents/ ehc/ehc/ehc170.htm, accessed 19 August 2010).
- Kiely P, Yap D, De Brou GB, Fraser D, Dong W. Presented at the 90th air and waste management association. Toronto, Ontario: 1997. A comparative study of Toronto’s air quality and selected world cities. [Google Scholar]
- London: Department of the Environment; 1999. Airborne Particles Expert group, Source Apportionment of Airborne Particulate Matter in the United Kingdom. [Google Scholar]
- ILO, WHO, OSHA, DOSH-Malaysia, AIHA
- FA, HWR, MSW, EPA,CPCB
- http://www.epa.gov/air/criteria.html
- http://ec.europa.eu/environment/air/quality/standards.htm
- Effective Handling of Fluids and Liquid Metals Using IoT, Praveen Sankarasubramanian, Volume 3, Issue 1, January – March 20, International Journal of Institution of Safety Engineers (India)
- Md. Alamin., Hassan, Dr. Khondoker, Mahbub., “Life Cycle Assessment of Solid Wastes in A University Campus in Bangladesh,” Proceedings of the W aste Safe 2013 -3,d International Conference on Solid Waste M management in the Developing Countries 10-12 February 2013, KhuIna, Bangladesh.